Founded in 2017, the start-up Stirweld has developed a new friction stir welding system, which has the particularity of being installed directly on a machining center. His process makes it possible to divide the cost of accessing this technology by ten. Meeting with the CEO and the co-founder of the company.
Invented in the 1990s, Friction Stir Welding, also known as FSW for Friction Stir Welding, is a solid state welding process without the addition of filler metal. Since 2017, the start-up Stirweld has been developing a system to install this technology directly on a machining center. Its ambition is to democratize the use of FSW by dividing its acquisition cost by ten. Its system is the result of applied research work within the Maupertuis Institute and the École Normale Supérieure in Rennes. Located on the outskirts of Rennes, the company markets its FSW welding process all over the world. Interview with Laurent Dubourg, CEO and co-founder of Stirweld.
Engineering Techniques: How does FSW welding work and what is its interest?
Laurent Dubourg : This is a cutter that rotates and is plunged into the parts. Friction causes heat and helps to mix and knead the two parts to be welded. This technology works with ductile materials such as aluminum, copper, magnesium, tin and lead. It represents a revolution in the welding of aluminium, a very complicated material to weld. Conventional welding, of the TIG (Tungsten Inert Gas), MIG (Metal inert gas) or laser type, in fact causes several defects with problems of porosity, sticking, cracking, and a sharp drop in mechanical resistance. Thanks to the FSW, we manage to cancel these defects, because the welding is carried out up to a temperature of 500 degrees, while the melting point of aluminum is at 600 degrees. Since one heats up much less, the material is almost not degraded.
How did you manage to adapt this technology to a machining center?
We add four functions on machine tools. First of all, force control, because FSW welding requires constant pressure to be applied to the part, whereas in machining, the position remains constant. To solve this problem, we have integrated a piston which goes up and down and whose role is to ensure constant pressure and a plating of the tool on the part.
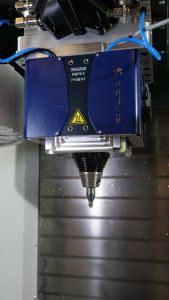
Then, a tool cooling system was integrated to prevent it from heating up and the temperature reaching the melting point of the material, while still welding in the solid state. To overcome this difficulty, we have integrated a double cooling of the head, with water and air, associated with temperature sensors.
The purpose of the third function is to protect the machining center once morest welding forces and vibrations which might damage it. Regarding the forces, we have added three bearings in the head, whose role is to support the welding forces, then to transmit them directly into the solid structure of the machining center. For vibrations, I prefer not to make our technological solution public, for reasons of confidentiality.
Finally, the last function concerns quality control. Our head is equipped with sensors that record the force and different temperatures to allow us to carry out a 100% control of the quality of the weld being welded.
What are the benefits of your technology solution?
Our process costs €97,000, whereas it costs almost a million euros to use FSW with our competitors. By dividing its acquisition cost by ten, our ambition is to democratize this technology, the price of which has until now been the main obstacle to its use. Then it remains to make it known and to train people. This technology is still little known, because it is new, but I think the same thing will happen with metal 3D printing, an area in which I did my doctoral thesis. 10 years ago, apart from a few experts, nobody knew regarding this technology, whereas now it is present in all trade fairs. There is, however, a difference between these two technologies: the parts manufactured using our FSW welding process cost less than other existing solutions, which is not the case with metal 3D printing.
Then, FSW welding will partially compensate for the lack of manpower, by automating the welding. In the next 5 years, there will be a shortage of approximately 400,000 welders in Europe and the same number in North America. This is a disaster for the industry. Thanks to our technology, the need for an operator will be less important, and in addition the skills sought are shifted, since we will be recruiting more machining center programmers.
To whom do you market your process?
There are a wide variety of industries that may be affected by FSW welding. Today, we have marketed 32 FSW heads all over the world, including 7 in France. Our top three customers in France are Ariane, Valeo and Airbus. At Valeo, our process is used to weld electrical boxes that regulate car electric motors. Our process is also used to weld certain electric car control boxes from the manufacturer Tesla in the United States. For Airbus, our technology will be used to weld the tanks in which liquid hydrogen will be stored at cryogenic temperature for their future aircraft. These tanks are made of aluminum and FSW welding is the most efficient for this type of material.
What are the prospects for your business?
We are in a phase of very strong growth, since we plan to market 24 FSW heads this year. At the moment, we are installing a head in South Korea, and another soon in Mexico. We deliver to our customers and train them in the use of our process. For now, we are the only company in the world to offer the use of FSW on a machining center, and we have protected our technology with a worldwide patent. But we know we’re going to be copied, and innovation is a constant race, so don’t rest on your laurels. In 2017, we launched our first standard FSW head, and since then we have developed three new heads, with new functionalities for our customers. One of them is a retractable head, to avoid that at the end of an FSW weld, when the tool withdraws from the part, it leaves a hole. In 95% of applications, we have different solutions so that this defect is not apparent. On the other hand, on hydrogen tanks, it can lead to a leak. We have therefore developed a retractable pin head which allows the hole to be closed. We continue our R&D work in order to release new versions of FSW heads.
Illustration credit of one: frimufilms