The more than thirty participants in the Flam3D event Start to 3D print have already received a preview of what they can expect in the field of additive manufacturing at Machineering. MT3D demonstrated the effect of design for AM on both machine part cost and performance. Desktop Metal dealer Buhlman addressed the question of how to improve the accuracy of binder jetting.
The setting for Flam3D’s event, co-organized with Seido Systems and Industrial Fairs, mightn’t be more appropriate. While the industrial 3D printers from Seido Systems printed parts – the showroom is also part of the production space for sister company Seido Solutions – the participants were familiarized with what 3D printing is, the technologies, but above all how to use the technology.

Design fo AM broadens the application area of metal printing
There were practical cases from the members. Willem Van Cauwenberge, head of engineering at MT3D, a metal printing service company, made clear the impact of design on the basis of a concrete application from machine construction. It concerns a part that MT3D 3D prints in batches of regarding 100 pieces for a machine builder, who previously assembled the part from several components. MT3D first of all reduced this to 2 more parts. “Less assembly means less costs,” says Van Cauwenberge regarding one advantage for the machine builder. Through several design iterations, MT3D has succeeded in reducing part printing time by 20%, eliminating support structures and therefore avoiding post-processing. “And this improves the reliability of the AM process.” MT3D in Kuurne now prints on four metal 3D printers, two from Trumpf and two from Eplus 3D.
During Machineering, Willem van Cauwenberge will also use this machine part in his Expert Class on Friday 31 March. Then he elaborates on how the right design choices metal 3D printing is suitable for many more applications and can compete with conventional processing methods.
Improve accuracy with Desktop Metal
Brice Buhlman (Buhlmann NV) showed the possibilities of weight savings in mechanical engineering by using 3D printing. He also elaborated on how to increase repeat accuracy on Desktop Metal’s systems when needed. By default, the Shop System achieves a geometric deviation of less than 1% following sintering by simulating the sintering process in the software beforehand. Subsequently, during printing, this distortion is compensated for. “If we need higher accuracy, we combine a 3D scan with simulation,” says Brice Buhlmann. Then the deviation is limited to less than 0.3%. During Machineering, application engineers from Desktop Metal will be present at the Buhlmann stand, one for 3D metal printing and the other for plastics. Perhaps a third application engineer from Desktop Metal will come for sand printing for the casting industry. Buhlmann will also be demonstrating the new version of SoilidCAM at the Brussels fair, which combines additive and subtractive manufacturing in one software package.

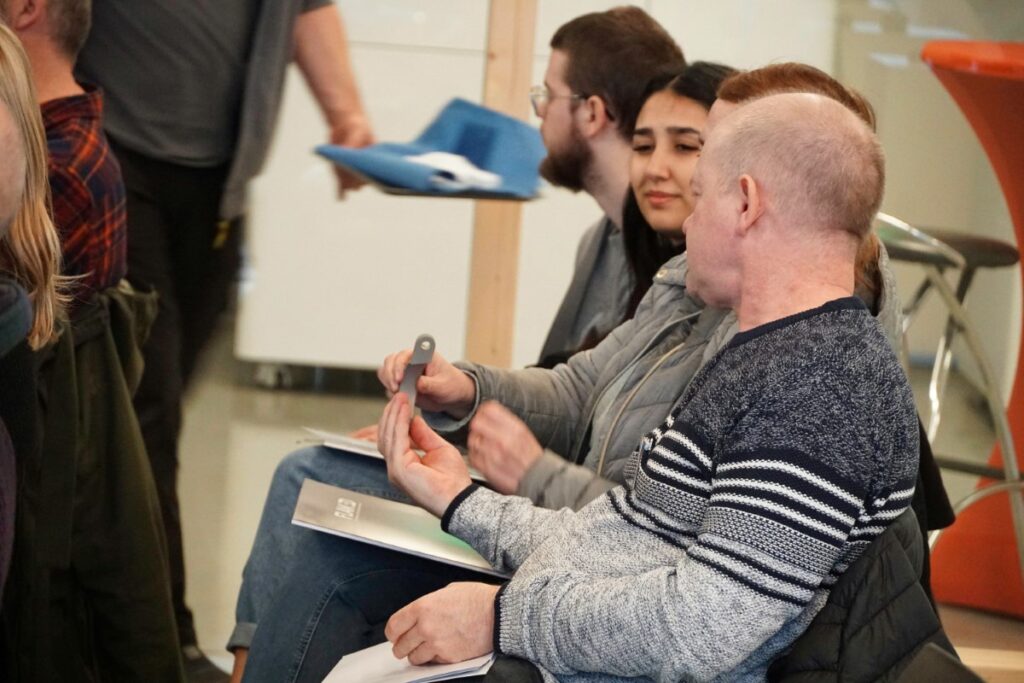

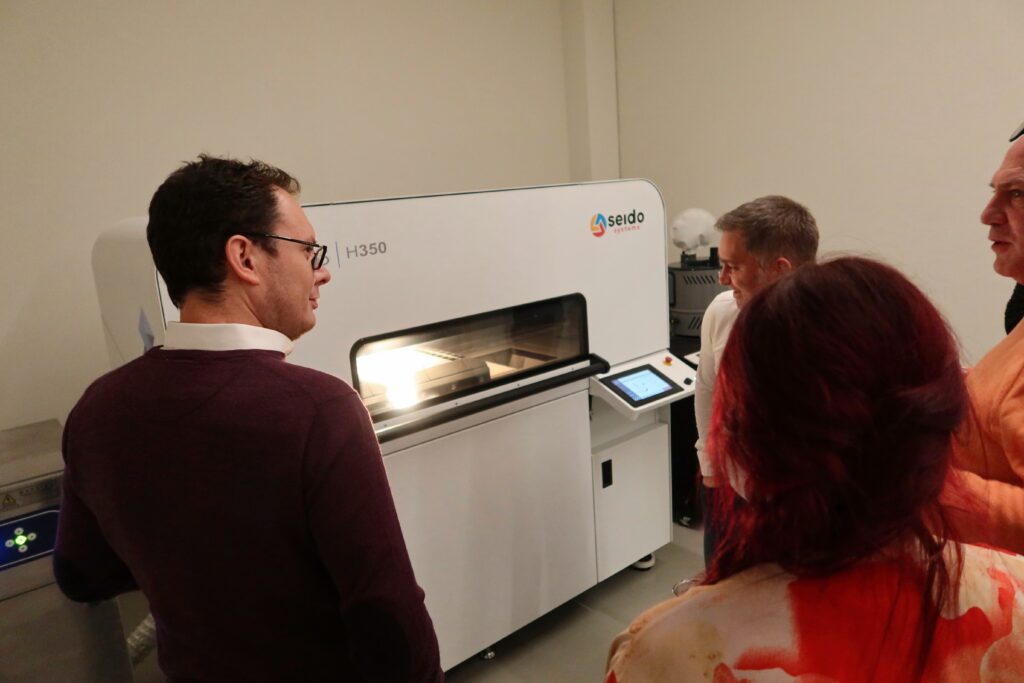
Clockwise: Brice Buhlmann, Desktop Metal demo piece goes around, the Genera G2 DLP printer and below a demonstration of the Stratasys SAF H350 printer.
AM Solutions, also an exhibitor at Machineering, presented the various solutions to partially automate post-processing during the Start to 3D print event. This concerns both de-powdering and improving the surface quality.
More regarding the event at Seido Systems next week
Machineering will take place from March 29-31 at Brussels Expo. Tickets are available for free with access code 105.
URL Copied