In today’s hyper-connected world, the demand for advanced antennas has never been greater. As 5G networks expand and the groundwork for 6G begins, industries are pushing the boundaries of innovation to create antennas that are not only faster and more efficient but also lightweight and cost-effective.At the forefront of this revolution is additive manufacturing, a cutting-edge technology transforming how antennas are designed and produced. Leading this charge is Xiaoyu (Rayne) Zheng, an associate Professor at UC Berkeley, whose team has developed a groundbreaking 3D printing platform poised to reshape the future of antenna manufacturing.
The global antenna market is on a remarkable growth trajectory. According to Mordor intelligence, it is projected to reach $34.24 billion by 2029, growing at a steady annual rate of 7.8% between 2024 and 2029. Antennas, often overlooked, are the backbone of modern dialogue systems, enabling everything from IoT devices to satellite networks. these critical components must be compact,lightweight,and capable of handling high-speed data transmission. While conventional manufacturing methods like machining have been the norm,3D printing is emerging as a game-changer,offering the ability to create intricate lattice structures that reduce weight without sacrificing performance.
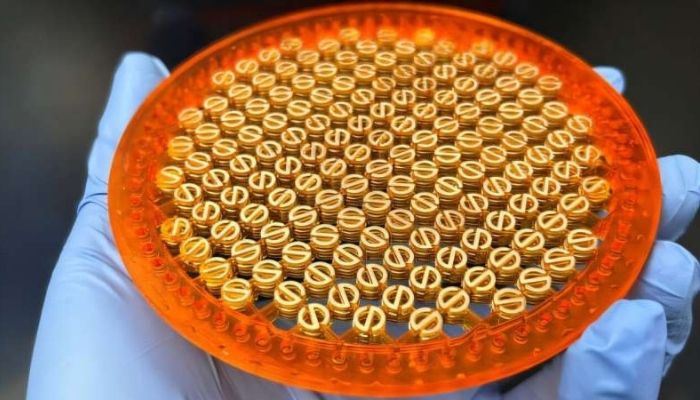
Phase gradient emission grating with three layers of interpenetrating S-rings and dielectric materials (photo credit: X. Zheng)
Overcoming the Challenges of 3D Printing Antennas
Table of Contents
- 1. Overcoming the Challenges of 3D Printing Antennas
- 2. Revolutionizing Antenna design: How 3D Printing is Shaping the Future of Telecommunications
- 3. the Breakthrough: 3D Printing Meets Antenna Design
- 4. Why This Matters: The Impact on Industries
- 5. Challenges and the Road Ahead
- 6. Join the Conversation
- 7. How Additive Manufacturing is Transforming Antenna Design
- 8. The Power of Precision: 3D Printing in Antenna Fabrication
- 9. Additive manufacturing: A Game-Changer for the Antenna Market
- 10. Challenges and Opportunities in 3D-Printed Antennas
- 11. The Future of Antenna Design: Limitless Possibilities
- 12. Conclusion: A New Era in Communication Technology
- 13. How does Conformal Printing Deposition (CPD) contribute to overcoming limitations in traditional antenna fabrication?
- 14. Key advancements in 3D-Printed Antennas:
- 15. Challenges and Future Directions:
- 16. Industry Impact:
- 17. Join the Conversation:
While 3D printing holds immense promise, it is not without its challenges.current additive manufacturing techniques often force manufacturers to choose between all-dielectric or all-metal antennas, limiting their versatility. even when combining materials is absolutely possible, the process typically involves complex post-processing steps that undermine the efficiency of 3D printing. These limitations have hindered innovation, creating a gap that Zheng and his team are determined to bridge.
Their solution is a revolutionary 3D printing platform called “charge programmed multi-material 3D printing” (CPD). Zheng explains, “The new platform is a global system for rapid production of nearly all 3D antenna systems. It can pattern highly conductive metals with a wide range of dielectric materials.” this breakthrough technology enables the seamless integration of diverse materials, paving the way for antennas that are lighter, more efficient, and capable of meeting the demands of next-generation communication systems.
The implications of this innovation are profound. By eliminating the need for cumbersome post-processing and enabling the creation of complex, multi-material structures, CPD has the potential to accelerate the development of advanced antennas. This could lead to faster deployment of 5G and 6G networks,improved IoT connectivity,and enhanced satellite communication systems.
As the world becomes increasingly reliant on wireless communication, the role of antennas will only grow in importance. With pioneering technologies like CPD, the future of antenna manufacturing looks brighter than ever, promising a new era of connectivity and innovation.
Revolutionizing Antenna design: How 3D Printing is Shaping the Future of Telecommunications
Imagine a world where antennas are no longer bulky, rigid structures but lightweight, intricately designed components capable of unprecedented performance. Thanks to groundbreaking advancements in 3D printing,this vision is becoming a reality. Researchers are now leveraging additive manufacturing to create antennas with complex geometries and enhanced functionality, paving the way for innovations in telecommunications, aerospace, and beyond.
the Breakthrough: 3D Printing Meets Antenna Design
At the heart of this revolution is a cutting-edge technique called Conformal Printing Deposition (CPD). This method uses stereolithography to deposit photopolymers in precise locations, forming a 3D mosaic. These photopolymers attract metal ions during the plating process, allowing for meticulous control over the antenna’s design. As Dr. Xiaoyu (Rayne) Zheng, a leading researcher in the field, explains, “It allows essentially any complex 3D structure, including complex lattices, and has demonstrated deposition of copper with near pristine conductivity, as well as magnetic materials, semiconductors, nanomaterials, and combinations of these.”
This breakthrough is not just about creating intricate designs; it’s about redefining what’s possible. By integrating diverse materials into a single 3D structure, researchers can now produce antennas with unparalleled complexity and functionality. This opens up new possibilities for industries that rely on high-performance antennas,such as 5G and 6G telecommunications,satellite systems,and IoT devices.
Why This Matters: The Impact on Industries
The implications of this technology are vast. Traditional antenna manufacturing methods, such as machining, often result in heavier components and limited design adaptability. In contrast, 3D printing enables the creation of lightweight, lattice-like structures that maintain—or even enhance—performance.This is notably crucial as industries demand faster, more efficient, and cost-effective solutions.
Dr.Elena Martinez, a leading expert in additive manufacturing for antenna design, highlights the meaning of this shift: “With 3D printing, we can create intricate lattice structures that are not only lightweight but also maintain—or even enhance—performance. This is critical as industries demand antennas that are faster, more efficient, and cost-effective.”
From enabling faster data transmission in 5G networks to improving signal strength in aerospace applications,the potential applications of 3D-printed antennas are limitless. Moreover, the streamlined manufacturing process could significantly reduce production costs, making advanced antenna technology more accessible to a broader range of industries.
Challenges and the Road Ahead
While the advancements are promising, challenges remain. One of the primary hurdles is scaling the technology for mass production. Currently, the process is highly precise but can be time-consuming. Researchers are working to optimize the manufacturing process,making it faster and more accessible without compromising quality.
Another challenge lies in material compatibility. While the CPD process has demonstrated success with materials like copper and magnetic alloys, integrating other materials—such as semiconductors and nanomaterials—requires further exploration. Overcoming these obstacles will be key to unlocking the full potential of 3D-printed antennas.
Join the Conversation
What are your thoughts on the role of 3D printing in antenna production? Do you see this technology transforming other industries as well? Share your insights in the comments below or connect with us on LinkedIn, Facebook, and Twitter. For the latest updates on 3D printing and other cutting-edge technologies, subscribe to our free weekly newsletter or explore our video library on YouTube.
To dive deeper into the research, the full study is available here.
How Additive Manufacturing is Transforming Antenna Design
In the rapidly evolving world of communication technology, the demand for compact, high-performance antennas is skyrocketing. Enter additive manufacturing—a groundbreaking approach that is reshaping how antennas are designed and produced. With the global antenna market projected to reach $34.24 billion by 2029, experts like Dr. Martinez believe that 3D printing will play a pivotal role in driving this growth.
The Power of Precision: 3D Printing in Antenna Fabrication
One of the most exciting advancements in this field comes from Professor Zheng’s team, who have developed a platform for designing and fabricating antennas with intricate geometries.Their work with phase gradient emission gratings—structures that combine interpenetrating S-rings and dielectric materials—showcases the potential of 3D printing. These antennas are not only compact but also capable of handling high-speed data transmission, a critical requirement for next-generation communication systems.

Additive manufacturing: A Game-Changer for the Antenna Market
According to Dr. Martinez, additive manufacturing is set to revolutionize the antenna industry. “The ability to rapidly prototype and produce custom antennas at a lower cost is a huge advantage,” he explains.Beyond cost savings, 3D printing enables seamless integration of antennas into devices, a feature that is particularly crucial for IoT devices and satellite systems.As the demand for compact, high-performance antennas grows, additive manufacturing is poised to become the go-to solution for industries worldwide.
Challenges and Opportunities in 3D-Printed Antennas
While the potential of 3D printing in antenna design is immense,challenges remain. Dr.Martinez highlights material selection as a key hurdle. “Ensuring that the materials used in additive manufacturing can withstand environmental and operational stresses is critical,” he says. Additionally, scaling production while maintaining precision and quality presents another challenge. However, with ongoing research and technological advancements, these obstacles are expected to be overcome, paving the way for even more innovative solutions.
The Future of Antenna Design: Limitless Possibilities
What excites Dr. Martinez most about the future of additive manufacturing in antenna design is its limitless potential. “We’re moving toward a future where antennas can be fully customized for specific applications,whether it’s for smart cities,autonomous vehicles,or space exploration,” he says.Additive manufacturing allows engineers to push the boundaries of what’s possible, creating antennas that are not just functional but also integral to the design of the devices they serve. “It’s a thrilling time to be in this field,” he adds.
Conclusion: A New Era in Communication Technology
As additive manufacturing continues to advance, it is clear that this technology is paving the way for a new era in communication technology. From compact,high-performance antennas to seamless integration into IoT devices and satellite systems,the possibilities are endless. With experts like Dr. Martinez leading the charge,the future of antenna design looks brighter than ever.
“Additive manufacturing allows us to push the boundaries of what’s possible, creating antennas that are not just functional but also integral to the design of the devices they serve.”
— Dr. martinez
How does Conformal Printing Deposition (CPD) contribute to overcoming limitations in traditional antenna fabrication?
The integration of 3D printing into antenna design is undeniably revolutionizing the telecommunications industry.By leveraging additive manufacturing techniques like Conformal Printing Deposition (CPD),researchers are overcoming traditional limitations and unlocking new possibilities for antenna fabrication. This technology allows for the creation of complex, multi-material structures that are lightweight, efficient, and highly functional—qualities that are essential for next-generation dialogue systems.
Key advancements in 3D-Printed Antennas:
- Complex Geometries: 3D printing enables the production of intricate designs, such as phase gradient emission gratings with interpenetrating S-rings and dielectric materials. These structures are compact yet capable of handling high-speed data transmission, making them ideal for 5G, 6G, and IoT applications.
- Multi-Material Integration: The CPD platform allows for the seamless combination of conductive metals,dielectric materials,and even semiconductors. This versatility eliminates the need for post-processing and opens the door to antennas with enhanced performance and functionality.
- Lightweight and Efficient: Traditional manufacturing methods frequently enough result in bulky, heavy antennas. In contrast, 3D printing produces lattice-like structures that are lightweight without compromising performance, a critical factor for aerospace and satellite applications.
- Cost and Time Efficiency: By streamlining the manufacturing process, 3D printing reduces production costs and accelerates the development of advanced antennas. This could lead to faster deployment of communication networks and broader accessibility to cutting-edge technology.
Challenges and Future Directions:
While the potential of 3D-printed antennas is immense, several challenges remain:
- Scalability: Current 3D printing processes are precise but can be time-consuming. Researchers are working to optimize these methods for mass production.
- Material Compatibility: Although CPD has shown success with materials like copper and magnetic alloys, integrating other materials (e.g., semiconductors and nanomaterials) requires further exploration.
- Standardization: As the technology evolves, industry standards will need to be established to ensure consistency and reliability in 3D-printed antenna production.
Industry Impact:
the implications of this technology extend across multiple sectors:
- Telecommunications: Faster data transmission and improved signal strength for 5G and 6G networks.
- Aerospace: Lightweight antennas for satellites and aircraft,enhancing connectivity and reducing fuel consumption.
- IoT: Compact, high-performance antennas for smart devices, enabling seamless connectivity in the Internet of Things.
Join the Conversation:
The future of antenna design is being shaped by 3D printing, and its impact will only grow as the technology matures.What are your thoughts on this innovation? Do you see it transforming other industries as well? Share your insights and connect with us on LinkedIn,Facebook, or Twitter. For more updates on 3D printing and cutting-edge technologies,subscribe to our newsletter or explore our youtube channel.
To learn more about the research, check out the full study here.
The era of 3D-printed antennas is here,and it promises to redefine connectivity and innovation in ways we are only beginning to imagine.