Coextrusion processes consist of simultaneously flowing, within the same tool, several polymers with different characteristics, in order to obtain a multilayer laminated product combining the qualities of each of the constituent polymers (impact resistance, scratch resistance, aesthetic appearance, barrier properties), while achieving good adhesion between the different layers. The first requirement is to obtain a multilayer product at the outlet of the die, each of the layers of which is of uniform thickness. This will depend on the geometry of the die, the rheology of the different polymers and their processing temperature. The second requirement is to ensure good adhesion between the polymers while avoiding the appearance of instabilities between the different layers. The modeling of these coextrusion flows is an effective tool for predicting the thickness distributions at the die outlet as well as the velocity and stress fields inside the die which are at the origin of the interfacial instabilities. After a description of the different types of coextruded polymer products and the dies that make it possible to produce them, we propose models of increasing complexity, first applied to multichannel dies (supplied by different single-material extrusion dies) for which the actual coextrusion flow only occurs over a short distance in a simple geometry. The challenge is then to predict the pace and time of establishment of the velocity and temperature fields for Newtonian, pseudoplastic rheological behaviors, in isothermal then non-isothermal situations. We then focus on the case of “coextrusion box” dies in which the different polymers are assembled upstream of a die of complex geometry. The challenge is then, both to predict as previously the velocity, stress and temperature fields, but also the distribution of the different polymers in the die and at its outlet. These coextrusion situations are illustrated by concrete applications.
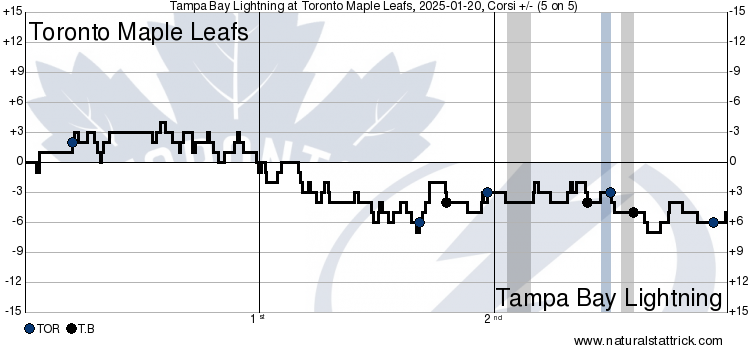