Cards 3D Printing Solutions presented the complete portfolio during a seminar. New in this is the technology of the British start-up Mayku, Thermo Pressure Forming. Not even 3D printing technology, but very useful in product development and single piece production. And 3D printing fits in seamlessly with it.
The portfolio of cards 3D Printing Solutions has expanded considerably. In addition to Ultimaker, which presented the Ultimaker S-line during the event, these are Nexa3D, Sinterit (in collaboration with GS Technology), Thought3D, which has developed an industrial filament dryer, and recently Mayku. For the British startup, the event in Best was one of the first times that it presented the technology directly to engineers.
Small batch production of plastic parts
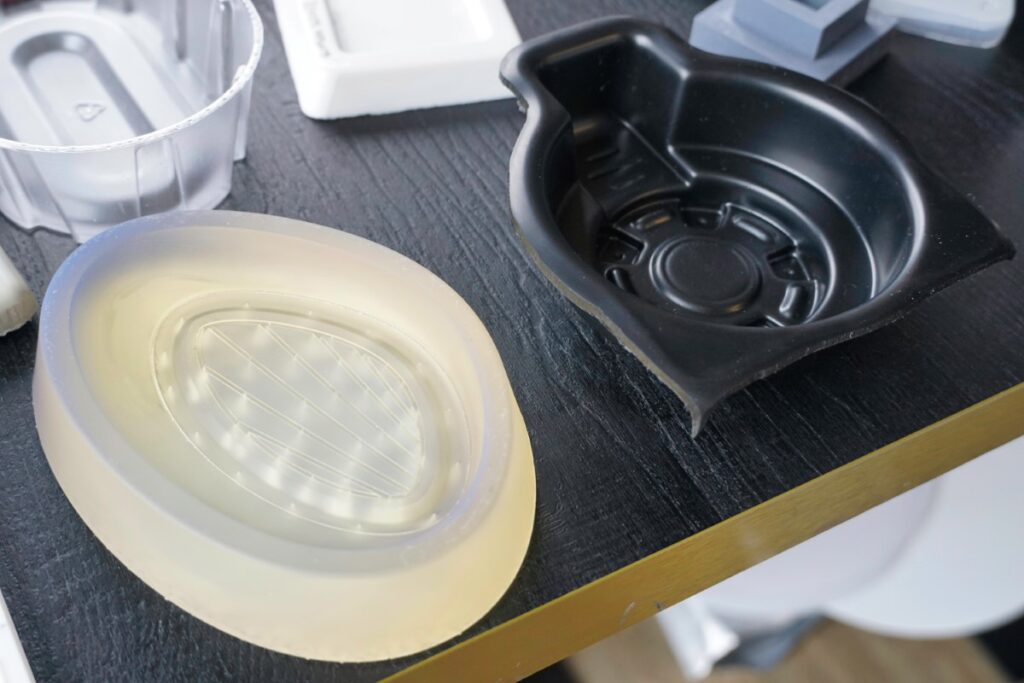
Detailing at sub-micron level
The Mayku Multiplier is similar to 3D printing, but is a completely different technology, namely Thermo Pressure Forming. Pressure forming is a well-known technology, which usually requires large production machines to form the plastic sheets under pressure and heat into the desired product. “We’re bringing this manufacturing technique to your desktop,” said Benjamin Redford, founder and CPO of Mayku. He founded Mayku seven years ago to make his vision of producing locally a reality. Pressure forming allows for finer details – sub microns – than vacuum forming, another thermoforming process. In Thermo Pressure Forming, a plastic plate is heated and then pressed around a mold at high pressure. The technology lends itself well to the production of single pieces up to a few dozen. The important advantage is that the end product has exactly the properties of the plastic.
Combination of 3D printing of the molds
The British startup has succeeded in reducing these usually large installations to a desktop model, which nevertheless heats the material to 200 degrees and has a clamping force of 5 tons. This forms plastic sheets up to 5 mm thick with product details better than 1 micron. At this point, the technology clearly differs from vacuum forming in that it works at a pressure four times higher. The molds are 3D printed, from polycarbonate for FFF printers or Nylon for SLA or DLP printers. The latter are preferred because of the finer detailing. Forming itself takes five minutes and is fully automatic. At the moment, Mayku has developed profiles for PETG, HIPS, ABS and EVA, a flexible material, and PMMA that is crystal clear. Mayku’s team is currently developing even more profiles, including for carbon-filled materials.
Mayku currently has a pioneer program for customers looking to push the boundaries of technology. They then work directly with the R&D team, which also supplies customized material profiles.
URL Copied