This might advance hydrogen as an energy carrier: Fraunhofer researchers have found a new way to convert hydrogen into methanol – without major energy losses. This might greatly simplify storage and transport.
The new methanol reformer is even significantly smaller than previous models.
Photo: Fraunhofer IMM
Hardly a day goes by without new developments being announced on the subject of hydrogen, and with good reason: its potential for the energy transition is enormous. And in fact, the concentrated efforts are leading to more and more innovations that will probably soon make the environmentally friendly energy source suitable for everyday use in many areas – the Fraunhofer Institute for Microtechnology and Microsystems IMM has now presented a new methanol reformer that is intended for mobile use and puts its predecessors in the shade.
Climate-neutral conversion of hydrogen into methanol
Of course, the idea of converting hydrogen into methanol is not new. Methanol is much easier to transport and, above all, can be stored for a long time. In other words: It would be possible, for example, to produce hydrogen using electricity from solar systems using the electrolysis process, then convert it into methanol and bring it to regions where the energy requirement cannot be covered by solar energy. The carbon dioxide required for methanol production might be taken from the atmosphere. An alternative would be, for example, the use of power plant gases (carbon dioxide capture). This means that the bottom line is that it would be possible to make the process climate-neutral. Because the CO2, which is released when the methanol is converted back into hydrogen, was previously removed from the atmosphere.
Expert is certain: In 10 years, the hydrogen car will be normal
In detail, a methanol reformer is required, which requires additional steam so that the methanol becomes hydrogen – and carbon dioxide. With a mobile reformer, this can also happen directly in a car. So far, what sounds so practical has been associated with a number of problems in practice. On the one hand, catalysts are required for the corresponding reactions. These are usually pellets of pressed copper zinc oxide powder that go into the reactor. However, their abrasion soils the fuel cell. In addition, the whole process is much too slow. But that’s not all. Because the process loses a lot of efficiency because the steam reforming reaction only works with heat. A lot of energy is lost here and at other interfaces.
New catalysts and shape for more efficiency in hydrogen conversion
The scientists at Fraunhofer IMM have now largely mastered these challenges. An important building block was improved catalyst technology. “We rely on catalyst coatings containing precious metals that do not cause any abrasion – similar to automotive catalysts,” says Gunther Kolb, deputy institute director and division head at Fraunhofer IMM. “Therefore, less catalyst material is needed. Since our catalyst materials also have higher activity, the required catalyst mass drops once more, as do the costs.” This has another advantage. With conventional reformers, by-products such as carbon monoxide are produced when the system is not utilized to capacity. The researchers say this is not the case with their new methanol reformer.
The next point is thermal management. Ultimately, the conversion of hydrogen into methanol and back into hydrogen should also take place efficiently in order to be able to use the energy carrier optimally. The scientists have put what is actually a fairly simple idea into practice and changed the structure of the reformer. First they coated plate heat exchangers with the catalyst material and formed stacks of up to 200 plates. If the gas now flows over it, it is in contact with the catalyst on the one hand and can be heated up well in the small channels on the other. In addition, the researchers use the waste heat, which makes the system very efficient overall.
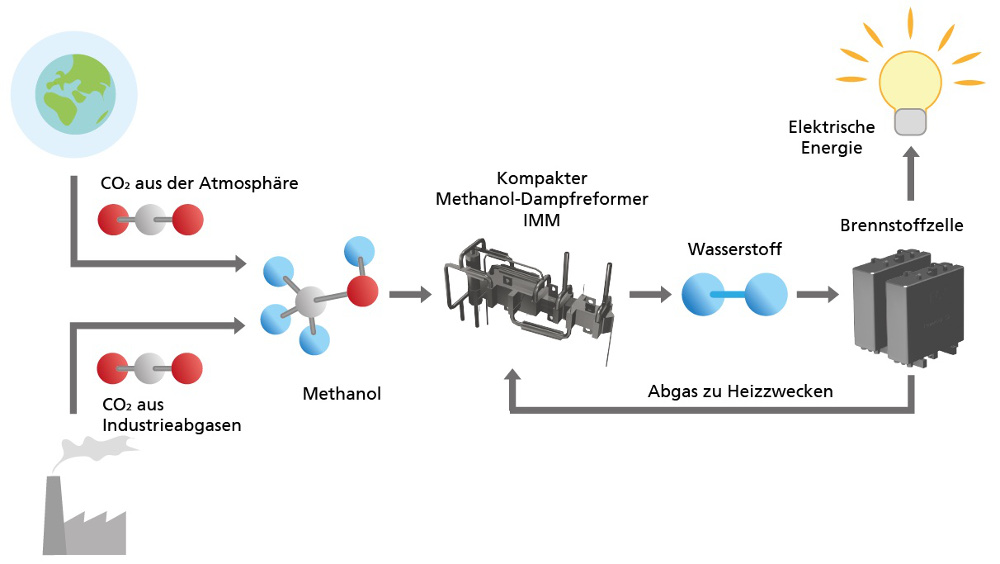
The illustration illustrates the simple principle of a methanol reformer. Hydrogen might be stored via this detour.
Photo: Fraunhofer IMM
Prototype of the methanol reformer suitable for series production
That sounds like a future-proof methanol reformer that might play a major role in hydrogen applications. The best thing regarding it: Its space requirement is just 17% compared to conventional reformers. The researchers are currently working on a prototype that should be ready in a few months. “The project is designed for the long term, and various prototypes are being integrated into land vehicles as a test,” says Kolb. He also has alternative materials in mind so that the reformers will weigh less for hydrogen storage in the long term – they are currently made of steel. According to Kolb, lightweight materials are also conceivable.
Incidentally, according to the researchers, the production can be compared to the manufacture of high-pressure heat exchangers for motor vehicles. So nothing stands in the way of series production.
Read more regarding hydrogen as a beacon of hope: