Chip makers trying to expand their manufacturing capacity will have to wait a year and a half or more for new chip manufacturing equipment to arrive, writes Nikkei Asia. The delays are caused by an unprecedented shortage of components that are needed to assemble this equipment.
Image Source: AFP / Jiji
Leading machine tool manufacturers for chip production, including Applied Materials, KLA, Lam Research and ASML, have warned their customers that they will have to wait 18 months or more for new shipments. This was reported to Nikkei Asia by several sources in the industry. The delay is related to the shortage of various components that are used to manufacture this equipment. There is a shortage of valves, optics, special pumps, microcontrollers, engineering plastics and various electronic modules.
At the same time, the demand for equipment for the production of microcircuits is growing. Taiwan Semiconductor Manufacturing Co. (TSMC), United Microelectronics Corp. (UMC), Intel and Samsung Electronics are building new factories, some of which should open as early as next year. According to sources Nikkei Asiathose plans may be in jeopardy. According to the same sources, the management of TSMC, UMC and Samsung went to negotiations with suppliers of production equipment in order to somehow expedite the resolution of this issue.
The delay in deliveries is growing at a rapid pace. If in 2019, before the start of the pandemic, deliveries took an average of three to four months, then in 2020 the delay was already 10-12 months. According to industry representatives, they faced “the worst delays in essential chip manufacturing equipment in decades”. For example, the delivery time for some test equipment of the American company KLA has increased to 20 months or more. Chip substrate production equipment can take up to 30 months to ship, up from 12 to 18 months last year, says Unimicron, the largest manufacturer of this critical component for chip fabrication. Others in the semiconductor industry who were interviewed also note the increased delivery time for the components they need. The situation is causing concern among both equipment manufacturers and chip manufacturers.
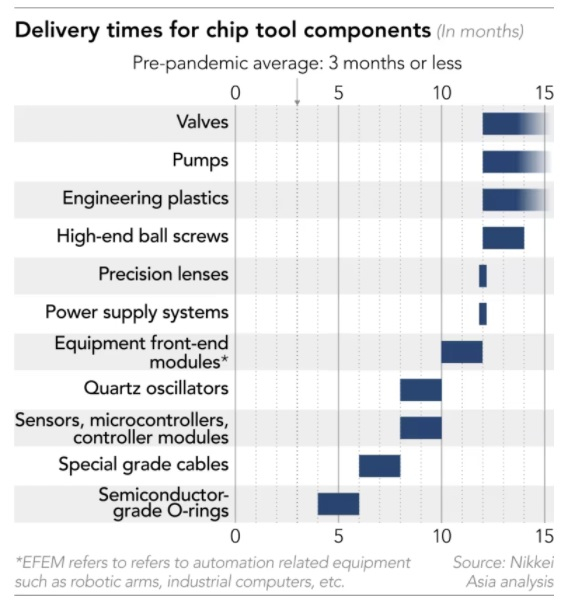
Scarce components for the production of equipment for the production of chips and their delivery time. Source: Nikkei Asia
“Last month a component supplier told us that their lead time was regarding six months. They also told us last week that the lead time had increased to eight months. And this week they said that deliveries were delayed up to 10 months. We don’t know what to think. We found ourselves caught in a vise between our chip-manufacturer customers and our component suppliers. The situation is very painful.”— one of the leading American manufacturers of equipment for the production of chips shared in a conversation with Nikkei Asia.
Applied Materials, the largest chip equipment manufacturer in the US, held an internal general meeting last month where its CEO urged employees to do everything possible to ensure the supply of components and chips for their machines.
TSMC, the world’s largest semiconductor manufacturer, has expressed concern over growing delays in new equipment shipments that might affect the completion of its new factories in the US, Taiwan and Japan. Previously reportedthat the company is already behind schedule on building its new US factory due to labor shortages and the coronavirus.
UMC, the world’s fourth largest contract chip manufacturer, confirmed in a conversation with the publication that it is sending its specialists to the offices of American and European equipment suppliers. However, UMC also added that they do not hope for a speedy solution to the problems that have arisen.
“According to our suppliers, the situation with the shortage of critical components is still getting worse. No positive changes are to be expected until at least the second half of 2022.”— commented the financial director of UMC Liu Chi-tung (Liu Chi-tung).
He also added that the lack of equipment might affect their expansion schedule in China’s Tainan. The company hopes that the launch of new lines will still take place in mid-2023, however, the equipment of these lines will obviously be slower than expected.
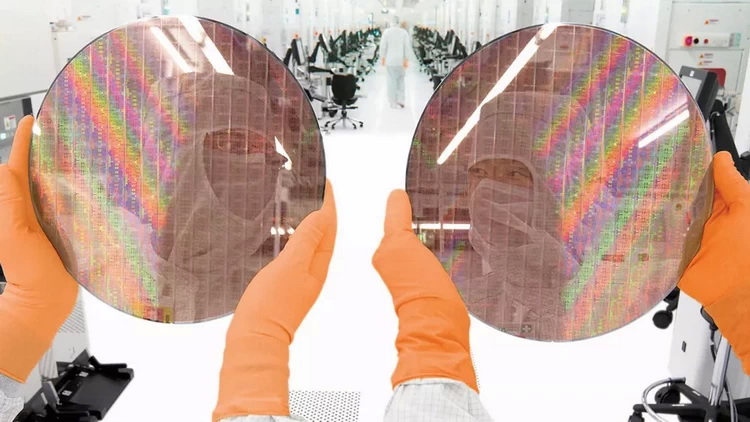
Image Source: GlobalFoundries
Everyone in the industry knows that chip shortages might last another two years, ASML said. But now the whole industry is working to solve this problem faster. At the same time, Nikkei Asia reports that at least 10 semiconductor industry representatives told the publication that many manufacturers of components for equipment used to manufacture chips have reported a reluctance to expand their capacity.
It will not be possible to replace the missing components and materials used to manufacture chip production equipment in the short term, several sources from the semiconductor industry say at once. Any alternative to parts already in use requires a lengthy verification process to ensure continuity of production and quality. Some components, especially those used in very delicate and precise applications, are produced by only a small number of companies. One of them, for example, is the Japanese Iwaki, which produces specialized pumps for working with chemicals. Another company is the German Zeiss, which manufactures high-precision optics. Finding suitable alternatives to their products is very difficult.
Many sources speaking to Nikkei Asia said that the current situation in the semiconductor industry is similar to that previously experienced by the automotive industry, which has experienced an increased demand for chips, which in turn, combined with supply problems, has led to significant shortages. As a temporary measure, automakers simply reduced their production volumes.
“The semiconductor industry has accumulated a lot of problems, ranging from the lack of components to logistics. And these problems continue to overlap. This is deja vu. The unprecedented crisis in the logical chains faced by automakers, computer component manufacturers and smartphones is now hitting the world’s chip makers.– added one of the leading American manufacturers of equipment for the production of microcircuits.
If you notice an error, select it with the mouse and press CTRL + ENTER.