2023-06-13 07:33:00
With Automatic Multilaser Alignement (AMA), Trumpf bridges the gap that has hitherto separated additive manufacturing from serial production. “With AMA we make the AM process reproducible, predictable and reliable. Together with our other solutions, we combine predictable quality with productivity,” said Marco Andreetta, Industry Manager General Industry at Trumpf’s AM division regarding this alignment tool.
Marco Andreetta knows the additive manufacturing industry from both sides. In 2007 he had to deal with it as a user; a few years later he switched to an OEM. And he recently started working as Industry Manager at Trumpf, with a focus on general industry. He describes his role as the linking pin between the market, the sales team and the R&D department. He talks to customers and translates their production needs into machine requirements. “I translate market trends and customer needs into requirements for the machines,” he summarizes.
With Automatic Multilaser Alignment (AMA), the lasers recalibrate themselves automatically
Stable process
Perhaps the greatest need expressed by customers is: ensure a stable, reproducible and predictable additive manufacturing process. “The biggest challenge in the coming years is how we bring additive manufacturing to series production. We need a stable and predictable process for that,” he says. With condition, powderbed and meltpool monitoring, Trumpf, like other machine builders, has taken steps in this direction. The missing link is: how do you correct for the inevitable thermal drift of the machine. Marco Andreetta: “For physical reasons, thermal drift occurs and that leads to incorrect alignment of the lasers at the end of the lengthy build job. With multilaser machines, which are needed for more productivity, you do not know exactly what is happening in the area in which lasers overlap.” With CNC milling machines you can still check with a measuring probe whether the machine is correctly calibrated; however, a laser is a non-contact tool.
AMA is a game changer, because it makes additive manufacturing a reliable and reproducible production process
Automatically re-calibrate
Trumpf has developed and patented Automatic Multilaser Alignment (AMA) for this. During the layer-by-layer construction of the metal workpiece, the lasers regularly re-calibrate themselves automatically. In the program, during the work preparation of the build job, you indicate every how many layers this must be done. Re-calibration is done with a marking that is printed, following which a high-resolution camera takes pictures and the software calculates how much the lasers need to be adjusted. “The maximum deviation following re-calibration is much less than half the beam diameter,” says Marco Andreetta regarding the accuracy that AMA provides. Measuring and re-calibrating only takes a few seconds, depending on the size of the workpiece. Trumpf’s Industry Manager calls AMA a game changer, because it makes additive manufacturing a reliable and reproducible production process. You can predict the quality in advance. “We are 100% sure of the mechanical properties, even in the areas where the lasers overlap.” The overlap areas are a problem with multilaser AM systems, especially during the production of critical end parts. If the lasers are not perfectly aligned, they will not properly melt the powder in such an overlapping area. Too little or too much energy can be applied if there is no proper alignment. In the early years of the Multilaser systems, this was solved by having each laser process a specific part of the workpiece. However, multilaser AM systems only make sense from an efficiency point of view if all lasers can cover the entire build plate, because then you can build on the same workpiece with several lasers.
Influence gas flux and galvo system
The use of Laser Powderbed Fusion systems as a production technology is partly determined by the efficiency of the galvo system in the 3D metal printer and the gas flux. Trumpf combines the group’s knowledge of the construction of machine tools and the development of its own laser sources to arrive at an optimal 3D metal printer. The fact that Marco Andreetta calls AMA a game changer has everything to do with the fact that a stable and predictable process is the basis for higher productivity, an industry requirement. “If you have a predictable process, you can move the process window. You can then use more energy, which increases productivity.”
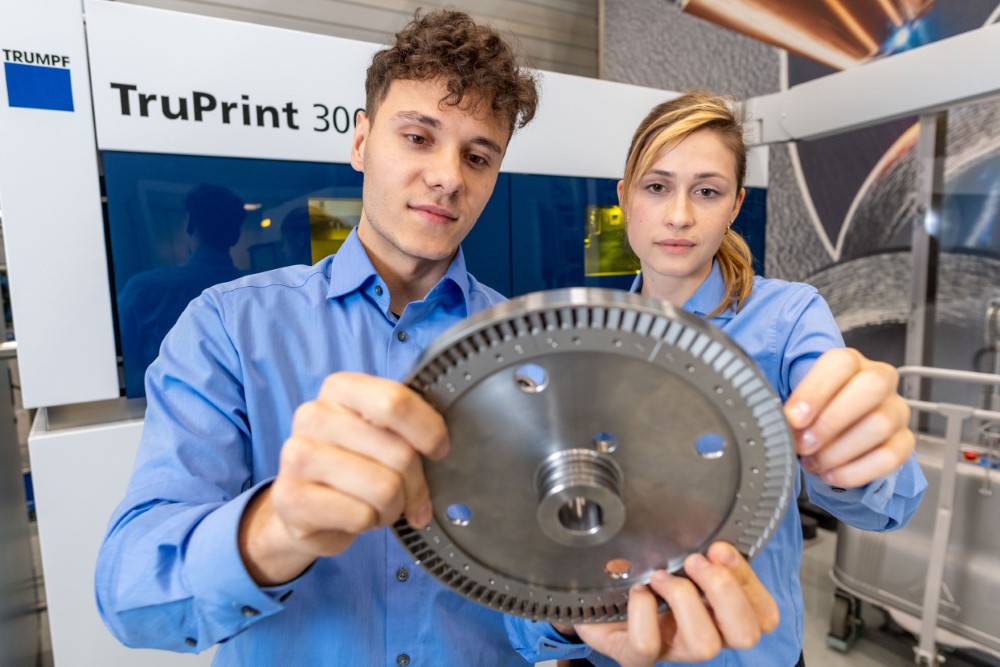
Where does Trumpf see opportunities in the industry?
Marco Andreetta is Industry Manager for general industrial applications, such as in the semiconductor, automotive and automation industries. He sees many opportunities for additive manufacturing in these industrial sectors. For example, anything related to cooling or fluid management can benefit from the design freedom of additive manufacturing. Hydraulic manifolds are one such application in which additive manufacturing is set to grow. “In the past, the surface roughness of internal channels was sometimes an issue. With Trumpf’s new build processor, we need less and less support structures. This increases the freedom of form and improves the surface quality of the ducts.” Heat exchangers, both for gases and liquids, are another application for which additive manufacturing offers opportunities. “With the refined optical elements, we can accurately dose the energy of the laser beam and we can print in aluminum walls thinner than 0.1 mm.” Andreetta expects the green laser with which Trumpf prints pure copper to open yet another growth market. Weight reduction through topology optimization will also lead to a growth in the number of applications. And finally, he points to the 3D printing of metallic glasses, amorphous metals, with the TruPrint 2000. For this Trumpf is working together with powder producer Heraeus AMLOY. This can lead to a whole new generation of sensors that can be printed or for medical components.
Marco Andreetta will give a presentation on Automatic Multilaser Alignement at the Manufacturing Technology Conference on 20 June. Manufacturing Technology Conference is an initiative of ASML and Thermo Fisher Scientific and is organized by Mikrocentrum. The event takes place in NH Koningshof in Veldhoven. In addition to the lectures and master classes, there will be round table discussions and regarding 75 companies will present their technology. More information and registration for a visit can be done via the website of the Knowledge Sharing Centre.
URL Copied
1687055876
#Automatic #recalibration #lasers #move #serial #production