Machine builders and high-tech OEMs are starting to embrace 3D printing
Machine builders and the high-tech industry in the Benelux are embracing additive manufacturing. This trend has been visible in plastics since the Covid19 lockdowns; on the metal side, the wrap is going on. What do the market leaders see happening?
AM for Production, Mikrocentrum’s new trade fair, will visualize the workflow of additive manufacturing as a production technique at the end of March. This provides a platform for sharing knowledge regarding how to use 3D printing as a production technique. The applications in the Dutch industry vary from ten to several hundred pieces on an annual basis to series of 100,000 parts. The latter group finds out that it might be smarter to order smaller batches more often. Parts on Demand has such a customer. They used to be hesitant to switch to 3D printing because of the large numbers that are needed on an annual basis. “With 3D printing, it makes no difference whether you order 100 or 1,000 pieces. As a result, the customer is much more flexible, because they can now change the design between orders,” says Neil van Es, CEO of Parts on Demand. The Utrecht 3D printing company has customers who have converted their entire injection molding work to 3D printing. And that work no longer goes to a low-wage country, but is produced in the Netherlands.
The supply chain problems of recent years have accelerated adoption
Read Solutions Magazine digitally
Acceptance has increased
You hear this trend more often. Marloes Homburg, sales and marketing manager at MakerPoint Digital Fabrication Solutions, sees printing end parts increasingly appearing in the requests for 3D printers. Together with the 3D printing of tooling, this is the application that customers from, among others, the machine construction industry think regarding the most. The reason: supply chain problems. Marloes Homburg: “Production times and costs are rising sharply and are becoming more unpredictable. Companies will then look for ways to produce parts in-house.” The acceptance of 3D printing as a production technique is increasing, notes director-owner of QDP, Maick Klaassen. “Three years ago we printed 70% prototypes and 30% finished parts, today it is exactly the other way around.” The company that also supplies injection molded products and molds also sees reasons other than supply chain problems, such as the use of lattice structures to make parts lighter yet strong. “Then there is no alternative.” Function integration is another reason he comes across. As an example, he gives hearing protection with an internal tesla valve geometry. “As an injection moulder, I wouldn’t burn my fingers on that. You then have to micro-injection mold and then ultrasonic weld or otherwise connect the parts. Now we print it in one piece.”
AM has gone from exploratory to a known process
Bram Grandjean
Growth of 3D metal printing
Although with some lag and on a different scale, you are currently seeing similar trends in the metal side of the AM industry. The Belgian company Melotte, one of the exhibitors at AM for Production at the end of March, was one of the first precision toolmakers in the Benelux to adopt 3D metal printing. In recent years, the supplier has noticed that AM projects return on a regular basis. “It has gone from exploratory to a known process,” says Bram Grandjean, account manager. Demand is higher at Wilting, which started using the first AM systems two years ago. Series production of manifold-like products is running on both systems. “Customers are increasingly recognizing how an AM component can improve the functionality of their machine, for example with regard to the flow of a gas or liquid or the heat capacity,” says Remon Haarsma, AM engineer. Demand is increasing to such an extent that Wilting expects to expand AM capacity this year, also because this offers the opportunity to offer stainless steel as a third material. KMWE also sees the demand for series production with additive manufacturing starting. That is why the supplier is investing in its own AM capacity this spring. Edward Voncken, CEO, believes the supply chain issues of recent years have accelerated adoption. For casting and forging parts for the aviation industry you are talking regarding lead times of 60 weeks these days. “With 3D printing, that is days rather than weeks.” In addition, the customer now orders the quantities that are required; not 100 pieces because the foundry uses that as the lower limit.

More flexibility
3D printing offers machine builders and other OEMs flexibility. The cost price may be higher for large numbers, but Neil van Es of Parts on Demand notices that the flexibility is also worth a lot. “If we have to print 100,000 parts, our cost price is higher than with injection molding. But they do have the option to adjust the design between each batch.” This allows them to respond more quickly to feedback from the market. Sustainability is another argument for opting for 3D printing, although customers often ultimately opt for the price and ignore sustainability.
From the expertise of the supplier, details can be added that improve manufacturability
Think early stage
At the high-tech suppliers of metal printed parts, function integration and performance improvement often play an important role. The suppliers prefer to sit down with their customers as early as possible to work with their customers’ design engineers, partly to improve printability and thus reduce costs. “It’s not wrong to let engineers play ping-pong in the design phase regarding what the effect is if you do this or that,” says Bram Grandjean. From the expertise of the supplier, details can be added that improve manufacturability, for example adding a rib to prevent deformation of the product due to the heat input. The design of the part has a lot of influence on the printability, more than with other production techniques. “If we are involved too late in the design process, more effort is required to make the part printable. And sometimes we conclude followingwards that more might have been done in terms of functionality,” says Adwin Kannekens, commercial director at Andra Tech Group, to which Wilting belongs.
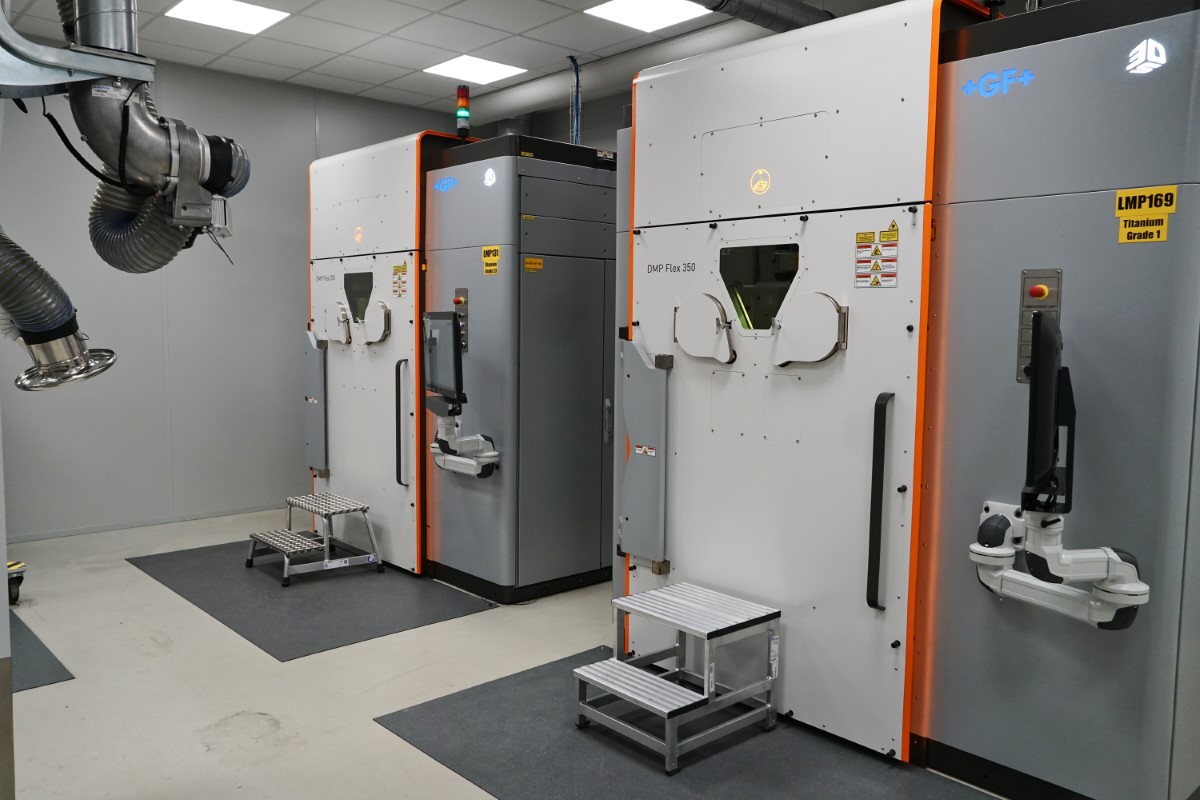
Cut costs
Thinking regarding the design is a balancing act on a thin rope. Rob van Loon, AM engineer at KMWE Precision, always wants to know what comes before and following the part that the customer wants to print. To see if parts can be integrated into one whole. He does this not only to save costs. “Sometimes you cannot achieve the requested tolerances per part, but you can with the composition.” Nevertheless, this remains a delicate consideration, says Adwin Kannekens. The cost savings in assembly are offset by higher costs in the AM process. “Ultimately, costs are euros at the bottom of the line for the customer.”
During AM for Production, visitors not only get an idea of the entire workflow that the exhibitors show, successful applications are also shown and AM experts share their knowledge and experiences in the lectures. AM for Production takes place on March 29 in the Brabanthallen in Den Bosch. More information: www.amforproduction.nl
URL Copied