Additive manufacturing by wire arc or WAAM is a technology derived from welding that uses standard arc welding equipment. It is therefore theoretically accessible to any company with an industrial welding robot! Here is a quick overview of the WAAM process.
In a previous article devoted to welding and cobotics, we mentioned the analogy between cobotics and additive manufacturing (AM), because like cobotics, AM is gradually leaving the laboratory to enter industry. , which is particularly the case with WAAM technology.
What is the WAAM process?
The WAAM process is a metal additive manufacturing process directly derived from welding, which consists of generating an electric arc between a substrate and a metal wire to form a bead.
There are few differences between robotic welding and WAAM, since we find the traditional welding torches that are used in industry for the assembly of parts. Nevertheless, technological improvements developed for welding make it possible to optimize the process.
This is particularly the case with CMT technology, developed by Fronius. We asked Guillain Hardy, welding engineer and project manager at Fronius International, to explain how it works:
“In WAAM, Fronius stands out with a technology called CMT, for Cold Metal Transfer. This consists of generating a very stable electric arc so as to produce less spatter during the removal phase and to limit the amount of energy supplied to the part. In CMT, the wire advances and retracts mechanically around 120 times per second, which cuts the electric arc and limits the heat input as the deposit forms. »
To learn more regarding CMT technology, we invite you to watch this video.
WAAM additive manufacturing has many industrial applications
Metal additive manufacturing is increasingly used for reengineering and reproducing parts that no longer exist. These technologies thus make it possible to continue to operate old machines, by reproducing parts traditionally made in foundries or by other processes, with reduced manufacturing times and costs for single parts or small series.
Moreover, like any additive manufacturing process, its strong point is flexibility and it becomes possible to manufacture parts with designs not accessible by foundry.
To increase productivity, it is also possible to use two current sources and two welding wires on the same torch. This is the case of the CMT technology’s Twin mode, which doubles the production rate and makes it possible to achieve deposition rates of the order of 10 kg/h.
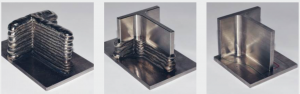
On the other hand, as with any additive manufacturing process, once the parts have been produced, post-processing by machining remains necessary in order to obtain parts with the desired dimensions. This robotic machining can be carried out directly following the manufacturing step, using a second robot, or in some cases, it can even be envisaged to implement it directly during the WAAM.
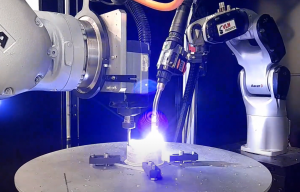
Here is an example of a bi-robot cell that combines additive manufacturing and in-process machining. The welding torch, attached to a robot, deposits the material on a rotary table and in parallel, another robot is used to machine the outer face.
The example of Naval Group
The industrial application that is currently the most talked regarding concerns the production of propellers for submarines and surface vessels, in particular by Naval Group.
For the production of propellers, WAAM manufacturing has many advantages over molding:
- good compactness of the material;
- no cracking problems[1] ;
- no shrink marks or residual sand particles from the mould;
- a reduction in costs and production times, compared to the foundry.
Furthermore, Naval Group seems to believe in this technology and is continuing its innovation work by adapting it to other metallic materials. A European project concerning the development of multi-material WAAM is also underway, the GRADE2XL project, with the aim of developing the change of filler metal during production in order to locally provide specific properties (mechanical, anti-corrosion, resistance friction…). This would thus make it possible to reserve “noble” materials, which are therefore more expensive, for certain specific areas, and therefore reduce manufacturing costs.
Applications in plastics: production of molds
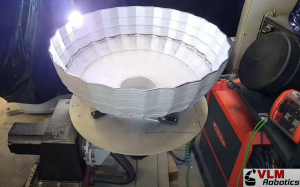
The WAAM is particularly suitable for the manufacture of large complex parts and in particular molds for the rotational molding of plastic parts.
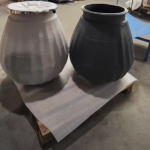
Fronius, for example, worked with VLM Robotics on a project to manufacture wine tanks by rotational molding. This type of part being difficult to implement in sheet metal work, in particular because of the presence of ribs on the part, WAAM manufacturing appeared to be an ideal solution, especially since machining was not necessary for this application.
A technology with a future!
Selon Guillain Hardy, “It is very difficult to have forged and stamped parts made in Europe, because there are few suppliers left and the know-how has been lost. Developing WAAM additive manufacturing cells to produce parts from a few grams to several tons thus makes it possible to find a competitive alternative on European soil. »
Given its advantages, WAAM technology should therefore continue to establish itself in the industry, although mass production is not yet relevant: “At the moment, the WAAM is not yet in series production and is mainly used for the production of prototypes. Large groups such as Naval Group, SNCF, ALSTOM and EDF are actively working on the subject as well as many universities and engineering schools. Training is also developing, as are aspects, certification and standardization. »
[1] Surface crack in a metal part