2023-05-26 06:30:18
Founded in 2015, the start-up Ways has developed an innovative process for drying wood in an enclosure saturated with CO2. It allows the wood to dry more quickly, improves its qualities, and is a means of storing CO2. Meeting with the director of business development.
For decades firewood or wood for the construction and furniture industry has been dried outdoors or in large sheds where the air is heated and then dehumidified to remove water from the pregnant. Created in 2015, the start-up Ways has developed an innovative technology for drying wood in an atmosphere saturated with CO2. This process makes it possible to dry the wood more quickly, improves its qualities, and is a means of storing CO2. Today, the company has entered an industrialization phase, since it plans to build a first demonstrator this summer. Interview with Olivier Pistiaux, the company’s director of development and associate of Ways.
Engineering Techniques: Can you present the technology developed by Ways?
Olivier Pistiaux: Wood drying has seen very few innovations in recent years, apart from vacuum drying, a process that is not suitable for treating large volumes and is relatively expensive. Our company brings a real breakthrough, since we dry the wood in an atmosphere saturated with C02. Our process works like traditional drying except that the heating needs are lower, because CO2 is more fluid and heat-carrying than air. The cell must still be sealed to be saturated with CO2, but operates at atmospheric pressure. Energy efficiency is optimized through a heat pump system. The enclosure is permanently dehumidified and CO2 is reinjected according to the quantity absorbed by the wood. For reasons of industrial secrecy, I cannot reveal more details regarding our technology.
What are the advantages of your process?
The drying is much faster. For example, the drying time of oak is achieved in 3 to 4 days, whereas it takes between 2 to 3 weeks in traditional dryers, and this, for the same drying quality. The moisture content varies according to the applications and is around 15% for wood intended for construction, and between 8 and 10% for furniture.
Then, drying under a CO2 atmosphere improves the quality of the wood thanks to the chemical transformations that take place during the process. For example, the surface hardness is improved and the knots harden, whereas they tend to jump during traditional drying. This quality is of particular interest to parquet manufacturers.
Finally, the drying takes place in a much more harmonious way and without deformation, whereas in the case of air drying, the wood tends to retract, and we see deformations and splits appear, which requires to sacrifice some of this wood on the sides. Thanks to the drying under CO2 atmosphere, there is almost no loss.
All these advantages have been demonstrated thanks to tests carried out in independent laboratories, in particular that of the Technological Institute FCBA (Forest Cellulose Wood-construction Furniture), and that of CRITT (Regional Centers for Innovation and Technology Transfer) Wood Occitania.
And what regarding CO2 storage in wood?
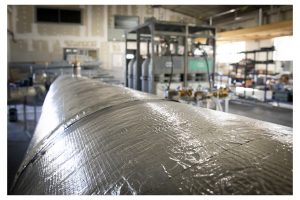
Several kilograms of CO2 are stored per m3 of wood, but we don’t know the exact number. Research work is underway to assess the exact quantity, in particular with the BIA (Biopolymères Interactions Assemblages), an Inrae laboratory. We also called on the CEA, which carries out analyzes using a method using nuclear magnetic resonance. The purpose of this work is more global and should enable us to understand in detail what structural transformations take place in the wood during the process and why its quality is improved. Even if we do not yet fully understand all these phenomena, our process is fully mastered and has been patented in 42 countries.
At what stage is the Ways project?
We have two prototypes in operation. The first is installed in a laboratory of an Air Liquide research center in the Paris region, which houses a start-up incubator called Accelair. The second, located in our premises in Rodez, is of the semi-industrial type and is 7 meters long. It has been installed for two years and has allowed us to fully control our process.
At the moment, we are entering an industrial phase, since GRDF has ordered a first full-scale demonstrator from us in the Paris region. It will be installed this summer next to a methanisation unit which produces both biomethane and biogenic CO2, which was until now released into the air. We are going to connect to this methanizer and use the CO2 to dry the wood.
In terms of R&D, we are adapting our technology to recover CO2 from industrial fumes. Unlike CO2 from a methaniser, adjustments have to be made since its concentration can vary and other gases are often present.
Upstream, other avenues of research are in progress. One of them concerns the reduction of wood treatment. We have good reason to believe that our process gives the wood better resistance to external attacks and is less easily attacked by insects and fungi. We are studying how our technology can reduce the quantities of biocides used during the wood post-treatment operation.
Another avenue of research concerns the potential applications linked to the ability of our process to very easily reach a humidity level of 0%, whereas this level is very complicated or even impossible to reach with conventional drying. We work with construction professionals to manufacture concrete-wood. This technique involves injecting wood into concrete to reduce the concrete’s carbon footprint.
1685165672
#technology #drying #wood #atmosphere #saturated #CO2