The French manufacturer metal 3D printers AddUp is part of the Metal3D project which aims to develop the first metal 3D printer for space. Led by the European Space Agency (ESA), it makes it possible to study the quality of parts manufactured in space, in a zero-gravity environment and more particularly on board the International Space Station. Airbus Defense and Space, Cranfield University and Highftech Engineering are also embarked on this adventure.
3D printing parts in space is no longer a dream and has been for a few years now. Machines capable of producing parts in microgravity have so far focused on plastic materials, offering the possibility of creating spare parts more quickly or other items necessary for the smooth running of a space mission. You can immediately imagine the time and cost savings achieved! The Metal 3D project, on the other hand, focuses on metals and shows encouraging progress.
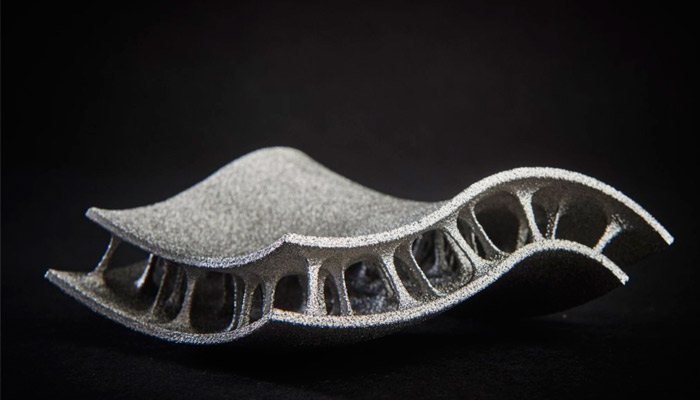
The European Space Agency commissioned this project (photo credits: Manufacturing Technology Centre/ESA)
Metal3D, a project involving several partners
In concrete terms, two machines have been developed: one which operates on Earth and another in space, within the Columbus module of the ISS. These 3D printers produce two batches of test specimens in two completely different environments. The objective for ESA is to characterize the mechanical properties of the material formed in microgravity. To carry out this mission, several industrial partners are involved. Airbus Defense & Space is responsible for integrating the components of the metal machine, ensuring their compliance for a space environment and their power supply. Highftech company focus on printer enclosure and fluid management. Cranfield University is responsible for the laser and stainless steel wire feed mechanics. Finally, AddUp is developing the entire internal structure of the machine, its mechanisms, but also software capable of communicating with the Earth and transmitting a certain amount of information to it.
Alexandre Piaget, R&D engineer at AddUp explains: “AddUp plays an important role in achieving this mission, but its involvement dates back to the pre-project phase where the feasibility of the project had to be demonstrated. This first part carried out in the premises of Salon de Provence laid the foundations of what the machine is today. In its final version, AddUp is in charge of moving axes, structural parts and machine software.”
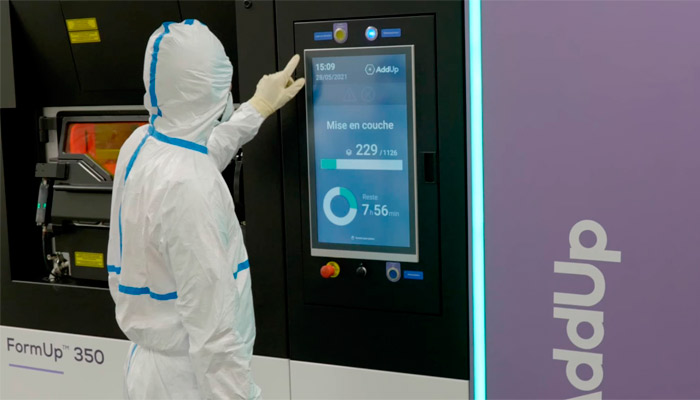
AddUp is currently developing PBF and DED machines (photo credits: AddUp)
Why a DED process?
The choice of a method of deposition of matter under concentrated energy is obviously not trivial. In the absence of gravity, the use of powder bed processes is extremely complicated either for safety reasons or for questions of shaping the powder in question. Turning to a DED machine, the partners rely on 316L stainless steel wire and a laser, a combination that promotes surface tension induced forces.
Finally, the press release states: The machine works under nitrogen in order to limit the oxidation of the material and to avoid the risks of combustion. Access to resources being limited in the ISS, the machine’s atmosphere is filtered and cooled throughout the manufacturing process to limit nitrogen consumption and recycle as much as possible of the nitrogen already present in the machine.«
We will not fail to keep you informed of the progress of this project! In the meantime, you can find more information in the video above. What do you think of the Metal3D project? Share your opinion in the comments of the article. Find all our videos on our channel YouTube or follow us on Facebook Where Twitter !
*Cover photo credits: NASA