2023-04-21 11:00:53
With the Fuse1 SLS printer, Formlabs has found the sweet spot: companies that do not 3D print a build full of parts every day, but that do have a weekly need for industrially applicable plastic parts in series of up to 1,000 pieces. For these companies, the ROI of the investment is often between 6 to 12 months. These are machine builders and supply companies that replace injection molding parts as well as milling and turning parts with plastic parts printed on the Formlabs Fuse.
Dennie Rijk, sales engineer at Formlabs dealer Visiativ 3D Printing, has since visited many manufacturing companies and machine builders in the Benelux. All but one had parts that lend themselves to production with the Formlabs Fuse1+ 30W. “This does not mean that the Fuse replaces other techniques. You see more and more hybrid solutions: companies integrate the 3D printer with traditional production techniques and partly outsource.”
Some machine builders replace their injection molded parts with 3D printing with SLS with Fuse1
Legion of applications
The applications are countless: from machine builders who will 3D print cable guides, air ducts, hinges and cover plates to a Dutch drone manufacturer that 3D prints the complete housings for electronics and thus insources the production. “We even have customers who now 3D print their injection molded products in quantities of up to 1,000 pieces per year on the Formlabs Fuse,” explains Dennie Rijk. The calculation is easy: you don’t have to invest in an injection mold and 3D print the parts that are needed for production next week.
Cheaper than milling or turning in certain applications
Visiativ 3D Printing, the new name for Layertec, also sees that the Fuse is becoming an alternative to CNC milling and turning in more and more companies. Depending on the part and application, this is up to five times cheaper than milling. Dennie Rijk: “The properties of the printed material are different from those of aluminium, for example. But for many applications nylon/polyamide (PA11) whether or not filled with carbon fibers is sufficient.” Aluminum has become a kind of standard material in mechanical engineering, but not because the mechanical properties are necessary per se. “Aluminum was cheap. And you can edit it easily. But there is often no need for aluminum as a material,” says the Visiativ 3D Printing sales engineer.
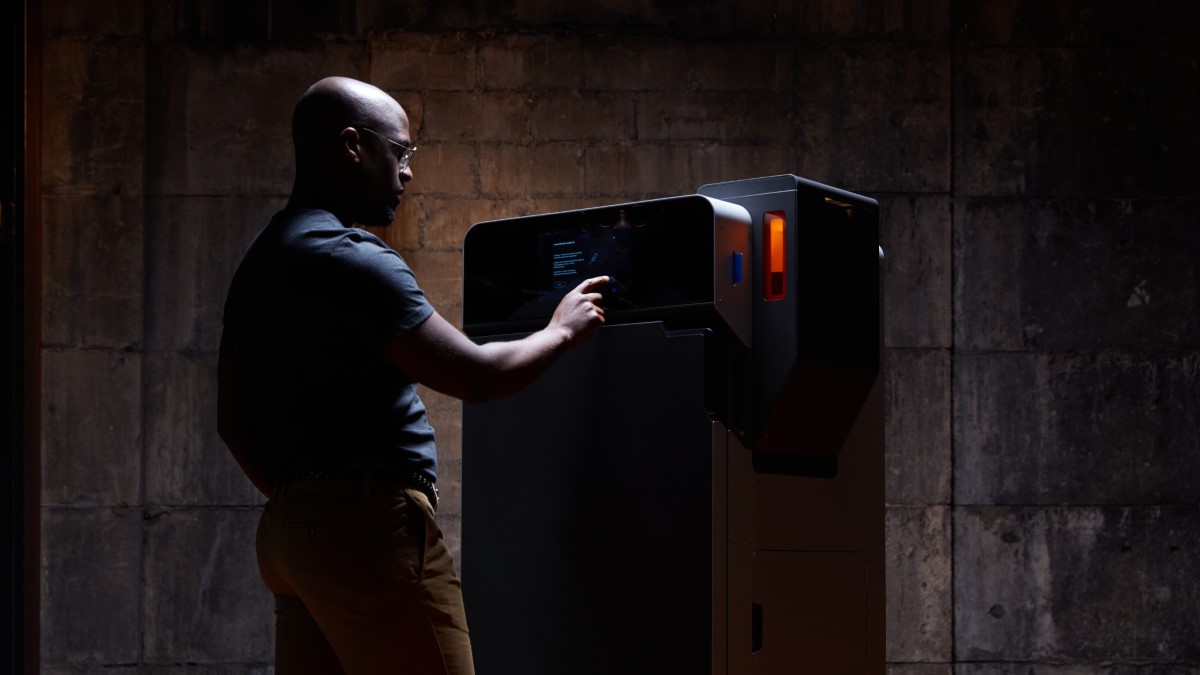

High accuracy
Dennie Rijk now has regarding two years of experience with the Formlabs Fuse. The first model, the Fuse 1, has been succeeded by the Fuse1+ 30W, with a more powerful light source. From the many benchmarks, the compact SLS 3D printer emerges as a machine with high accuracy and repeatability. “Also from machine to machine. Parts that you 3D print on different machines have the same tolerances. And they are really good.” For those looking for even higher accuracies, Formlabs has built an improved calibration algorithm into the firmware that allows users to easily calibrate accurately in the X and Y plane. The nesting software Preform that comes with the machine has also been improved. “The ultimate goal is to make Preform so good that you don’t need any external nesting software to achieve a very high density,” says Dennie Rijk. In terms of software, Visiativ will soon add nTopology, for which Visiativ has become a reseller. “Generative design, topology optimization, lattice structures and surface modeling will then be even faster and easier, including for even lighter parts.”
“With these new materials even more parties are discovering the difference between SLS and other techniques”
New materials
In addition to the hardware and software, Formlabs also supplies materials for the Fuse 1 (via the webshop). Formlabs also responds to the demand from machine construction with the materials. With the Fuse 1+, PA11 carbon filled has become available, because the light unit is stronger and the printer has a nitrogen connection. A new material is a TPU 90A, a flexible elastomer with a shore value of 90A, which makes it suitable for numerous applications in both consumer products and industrial parts. ‘With these new materials, even more parties are discovering the difference between SLS and other techniques,’ says Dennie Rijk. “If you are in the manufacturing industry, the Fuse is the better solution.”
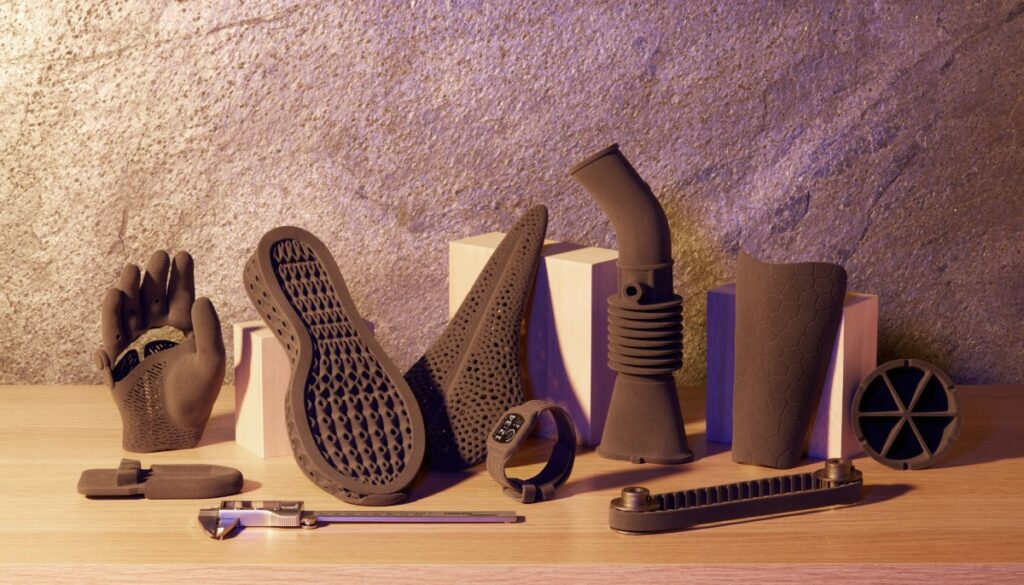
ROI from six months to a year
Yet he still notices hesitation at many companies: is the quality good enough? Can I print enough 3D? “Often the Fuse is looked at from an R&D department and not from the production side, while the profit can be made there. We have examples of ROI from six months to a year. What investment will this achieve? Dare to think differently.” Because experience shows that companies that once take the step to SLS printing, often expand following a while with a second or third Fuse SLS printer. These are relatively low investments because the unpacking and screening station, the Sift 1, can serve up to 4 or 5 printers. “Once companies have the Fuse, they can no longer live without it.”
Do you want to know more regarding the Fuse1? Click here or sign up for the roadshow organized by Visiativ 3D Printing and Formlabs on May 25. In it, customers share their experiences with the Fuse1
URL Copied
1682153195
#Formlabs #Fuse1 #brainer #machine #builders