The hundreds of plastic waste that are used daily and then scattered in the open air without having a definitive treatment for their disposal can have a sustainable path. It is regarding thermal cracking, an alternative that converts plastic into fuel.
It is the axis of the project that carries out a research group, emerged from the Neuquén Regional Faculty of the National Technological University, in Plaza Huincul.
The beginning of this proposal dates back to 2015 and, since then, there have been significant advances. The focus of the proposal is to give added value to the great problem that exists with plastics.
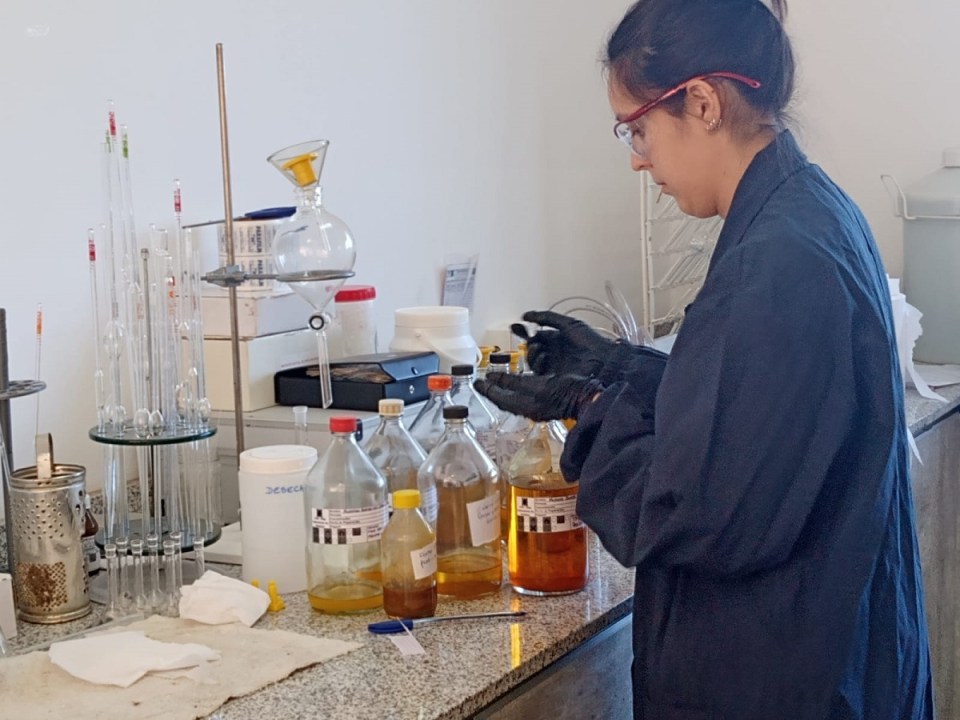
“The oceans are full of plastic, there are islands of this material that have the surface of up to seven times Spain. Not much is visible, but the reality is that they are full”, described the chemical engineer, Gabriela Shell, one of those responsible for the initiative from the UTN, in dialogue with BLACK RIVER.
The possibility of giving that added value to the plastic material and transforming it into diesel is the main reason for the thermal cracking project, through chemical recycling the final disposal of the plastic can be given.
“Plastics are long chains of carbon, enormously long and with cracking we are cutting them, depending on the temperature and pressure. It is given certain heat and it is cut in the amount of carbon that is needed, according to the fuel that you want to obtain”, explained Shell.
“Gases are obtained up to carbon 4, liquids from carbon 5 and when larger chains of 30 to 40 are made, solids are reached, even waxes, for example,” he explained.
It took the research group a year –from 2015 to August 2016- to reach the right temperature and pressure to obtain the diesel. It was trial and error until, at 360 degrees Celsius and up to 365 degrees and at a pressure of 0.50 to 0.70 kilos per square centimeters, they obtained the fuel: diesel.
They also reached a motorized gasoline that “is like a virgin gasoline” and non-condensable gases such as ethane, methane and propane that is nothing more than household gas. In the background, they also achieved a wax that can be used as a waterproofing for floors or footwear.
Shell described that, of all the fuels they obtained in the search process, diesel turned out to be the strong one because the plastic is already refined.
“The crude oil that arrives from Vaca Muerta to a refinery must undergo several prior treatments, for example. Among them, eliminate sulfur, which is one of the most important variables to banish. And plastic no longer has sulfur levels. This diesel would not need this process”, stressed the expert.
That diesel obtained in the plant will allow powering a generator; or intended for thermoelectric plants that use fuel oil and might be used as another module within refineries.
“There is a new concept that is biorefineries and this proposal would collaborate by making a certain fuel to derive it to another module, they can add it and obtain a more sophisticated product. It might also be in the chain of a refinery”, suggested the engineer.
The plant where the cracking process is carried out has the following dimensions: three meters high by three meters wide by three meters long, it is as if it were a cube. It consists of a reactor that is where the first batch is made with the 200 kilograms of plastic.
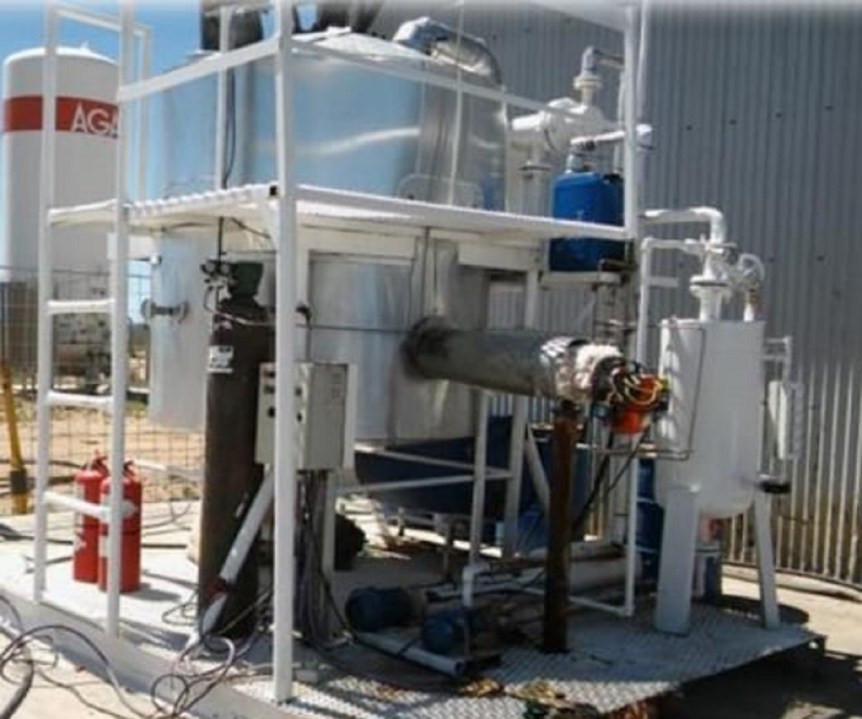
Heat is applied to it with a burner; the plastic melts until it reaches more than 360º and these gases rise towards an exchanger, condense, become liquid once more and remain in an accumulator.
Then, there are two pumps that take the production to a 200-liter tank and there the final raw product is obtained.
This product obtained is transferred to the laboratory at the UTN headquarters and distillation is carried out under the strict rules. There the diesel and virgin naphtha are obtained.
In the first experiments, they put the product achieved to the test when they tested it in the plant itself, which requires diesel for start-up.
“When we obtained the diesel itself, we tested it in a generator and found that it has an interesting octane number of around 95,” Shell said.
Currently, the plant of the initiative is located in a sector of the property that INVAP has in the Cutral Co technology park. While the laboratory used is in the headquarters of the Neuquén Regional of the UTN, in Huincul.
This year the own space was finished –inside the UTN university- and the expectation is that in three months it will be ready to be used. Furniture such as countertops, sinks, extractor hoods, and other furniture that will be provided by the municipality according to the commitment made by Mayor Gustavo Suárez is still missing.
the next steps
This year the agreement with the YPF company is expected to be put into operation so that tests can be carried out with equipment provided by the oil company. “We will see what other results these studies will give us to advance the research,” says the engineer who is also carrying out a doctorate at the Conicet with this project.
The first stage of the initiative was the construction of the plant. Five years from now, the plan is to be able to redesign it to have 4.0 technology and be automated, unlike the manual method it has now.
It will aim to obtain the fuel already at the plant and not take it to the laboratory. For this, a distillation column will have to be attached to the device, which has already been modeled and the number of necessary plates and the height have been calculated.
In this proposal are the Chemical Engineering scholarship holders: Gastón Pincheira; Sheila Tagliapietra; Alen Executioner; Michael Aguilera. The scholarship holders of the Electronic engineering degree: Gonzalo Contreras and Maximiliano Antío while the person in charge of the electronic area is Raúl Espinoza. While the doctoral student Shell is accompanied as director by Mónica Gramajo and Alberto Camacho as co-director.
The last stage of the process will be that both the plant and the laboratory are in the same space. The alternative is that it can be permanently installed in one of the chemical or technological parks in the oil region. Meanwhile, he might stay in a property belonging to the former Plaza Huincul workshops, in the Central neighborhood.
The expectations are that the tests in the laboratory will allow to improve the plant. “There were two donations from Techint in 2020 for 900,000 pesos and there we managed to buy devices: a touch screen, a 20 HP shredder to have greater shredding capacity, a larger fuel tank that complies with all safety measures, valves, we would improve performance, we would make the process more automatic,” he said.
Now, they received the second donation from the same company because they applied to a program of 2.5 million pesos for the purchase of a distiller that will go to the laboratory. This will make it easier to have the process more automated.
To comment on this note you must have your digital access.
Subscribe to add your opinion!
Subscribe