Startup from Rio Grande do Sul is developing an innovative solution for apple harvesting
Red, sweet and juicy, the apple that arrives to satisfy your hunger at snack time is the result of a complex process that begins with cultivation in the field and has, in the apple harvest, one of its most delicate stages. Sensitive, the fruit requires a series of care when it is removed from the tree and transported for packaging. Until today, this is a job done manually by orchards around the world — a seasonal task, which needs to be completed in a short period of time, requiring large movements to hire temporary labor — increasingly scarce and difficult to recruit .
Autofarm should present the technology for apple harvesting soon, and is already preparing for a new round of investments
A startup from Serra Gaúcha is adding expertise, knowledge and a lot of technology to seek the development of a solution capable of solving this challenging problem due to the complexity involving the apple harvest (and, later, also with the possibility of application to other similar fruits). The company Autofarm is working on equipment to automate the process of removing fruit from the apple tree — autonomously covering the orchard land and, using artificial intelligence, identifying the fruits, which are harvested by a mechanical arm with a flexible claw.
Labor shortages
“The apple harvest is one of the most complex points for the producer, especially in view of the increasingly latent bottleneck that is the lack of labor for the job. Finding and hiring temporary labor has been a real headache — a situation that occurs not only in rural areas, but in several other productive sectors. Faced with this impasse, Autofarm has been developing a project that intends to help the producer to automate the process, even allowing him to be able to scale his business in the future”, explains Tobias Grazziotin, one of the founders of the company, creator and executor of the project.
mobility in orchards
The equipment being developed features an autonomous platform, capable of geolocating and moving both via satellite and through vision cameras that map the environment, ensuring safety in the operation. In it, a six-axis robotic arm, known as an anthropomorphic robot, simulates the movement of the human arm. At the tip, a delicate flexible bottle is able to harvest without damaging the fruit.
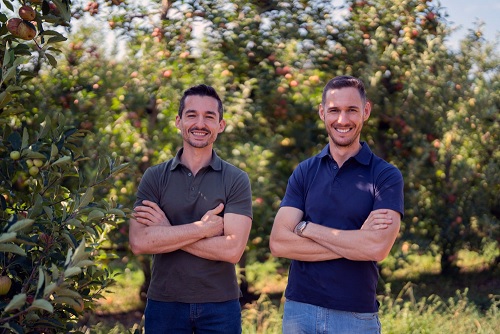
The final version will have four robotic arms capable of working simultaneously — which means the possibility of harvesting two apples per second at its maximum operating speed. In a harvest, it is estimated that a unit of equipment developed by Autofarm will be able to harvest 842 tons of fruit. “For the producer, this means savings of more than R$ 210,000 per harvest”, he explains.
Currently there are some companies around the world that seek to develop the same solution, but there is no commercially available equipment on the market that automates apple harvesting. There are auxiliary platforms that only facilitate the manual process. “This is because we are facing an extremely complex challenge.
We are adding a lot of expertise in mechanical engineering, robotics, Artificial Intelligence and a lot of innovation in the development of this solution”, says Grazziotin. Autofarm is an agtech startup from the company Fênix FabLab, from Caxias do Sul, controller and executor of the project. The initiative has two strategic investors, who, in addition to contributing resources, add technology and knowledge to the project: G&A Cemin Máquinas e Equipamentos Industriais, also from the same city, and Dalca Brasil, from Bento Gonçalves.
global opportunity
The project authored by Autofarm was submitted and approved by the Finep 2030 Business Program and awaits possible release of resources from this fund. Meanwhile, it is seeking investors from the private sector to make the next stages of development viable. The equipment prototype already exists and should be presented for the first field tests in March this year, during the apple harvest period in Serra Gaúcha. Its final version is expected to be completed within five years.
“It is indeed a challenging project. However, its market opportunities are enormous, in proportion to the complexity of the solution we are seeking to develop”, says Grazziotin. Brazil produces, on average, 1 million tons of fruit per year, with a harvest cost of approximately R$ 0.25 per kilo. In the world, there are 90 million tons/year, that is, a market of approximately 4 billion dollars. “For an automaker that comes to acquire the technology that we are developing, the market opportunities are extremely fertile, in the national scenario and mainly abroad”, guarantees Grazziotin.